Injection molding process, 13 common product defects and causes
1. Salivation
a. The material is not completely dried or the material is damp
b. The pre-molding speed (screw speed) is too fast
c. Nozzle temperature is too high
d. Bad return material (powder)
e. Insufficient suction volume
f. Insufficient nozzle contact force
g. Nozzle and mold sprue sleeve size does not match
h. Dirty nozzle contact surfaces (causing uneven surfaces)
Second, pre-plastic instability
a. The return ratio is unreasonable or unstable
b. Back pressure is too low
c. Long rod bridging
d. Material is wet
e. Unreasonable temperature at the cutting place (too high)
Three, flying edge
a. The parameter settings are not accurate (the transfer pressure point is too low, the holding pressure is too high, the firing rate is too fast, and the temperature is too high)
b. Dirty mold
c. Insufficient clamping force
d. Mold problem (damage)
e. Equipment problems (unstable pressure)
f. Nozzle temperature is too low
g. Uneven plasticization (long material rod, too fast screw speed, too low back pressure, etc.) cause cold material
h. The back suction is too small, causing the check valve to close unstablely
4. Insufficient mold filling
a. The parameter settings are not accurate (the transfer pressure point is too high, the holding pressure is too low, the firing rate is too slow, and the temperature is too low)
b. Dirty mold
c. The nozzle temperature is too low, the structure is unreasonable d. The check valve or the barrel is damaged
e. Gate, runner size is too small
f. Unclean return material (including miscellaneous materials)
g. Material is damp
h. Equipment problems (insufficient pressure)
I. The launcher is misaligned
J. The back suction is too small, causing the check valve to close unstablely
5. Insufficient mold filling from time to time
a. The rate of fire is too low (especially PA, POM)
b. For large products, the melt temperature is not enough
c. Uneven plasticization (back pressure is too low, speed is too fast)
d. Insufficient nozzle temperature
e. Damaged check valve or barrel
f. Impurities
g. Dirty mold
h. The material is not completely dried or the material is damp
I. The launcher is misaligned
J. The back suction is too small, causing the check valve to close unstablely
6. Focal spot
a. Dirty mold
b. The parameter settings are not accurate (the rate of fire is too fast)
c. The material is not completely dried or the material is damp
d. Too much clamping force
e. Mold problem (poor exhaust)
f. Too much suction
g. The barrel and the second joint are not sealed
7. Sag
a. Gate, runner size is too small
b. The nozzle opening is too small
c. Inaccurate parameter settings (holding pressure is too low, pressure holding time is too short, pressure transfer point is too high, material temperature or mold temperature is too high)
d. Uneven plasticization (back pressure is too low, speed is too fast)
e. For large products, the melt temperature is not enough
f. Check valve or barrel damage
g. The launcher is misaligned
Eight, product deformation
a. Wrong water connection
b. Product extrusion
c. Uneven product ejection
d. Insufficient cooling time
e. The rate of fire is too low
f. Too much pressure causes sticking
g. Uneven plasticization causes internal stress
h. Uneven mold temperature distribution
Nine, the size is unstable
a. Unstable parameter control (mold temperature, material temperature, holding pressure too low or too high, cooling time)
b. The material return ratio is unreasonable or unstable
c. Damaged check valve or barrel
d. The back suction is too small, causing the check valve to close unstablely
10. The weight is unstable
a. Inaccurate parameter settings (mold temperature, material temperature, holding pressure is too low or too high, cooling time, holding pressure time is not enough)
b. Nozzle temperature is too low
c. The dwell time is too short
d. Damaged check valve or barrel
e. Unstable material return ratio f. Unstable closing of check valve due to too small suction
Eleven, the product is easy to break
a. Melt temperature is too high or too low
b. Material wet
c. The rate of fire is too low or too high
d. The mold temperature is too high or too low
e. Weld line
f. Impurities
g. Uneven plasticization (back pressure is too low, rotation speed is too fast, long material rod is returned)
h. Mold sharp edges
i. Unstable return ratio
12. Weld lines
a. The rate of fire is too slow
b. Melt temperature is too low
c. Mold temperature is too low
d. Poor exhaust
e. Color masterbatch; uneven plasticization
f. Mold, product design is unreasonable
Thirteen, epidermis stratification
a. Material is wet
b. Miscellaneous materials
c. There is a problem with the color masterbatch
d. The rate of fire is too fast
Welcome to Suda Group, ISO9001 Certified
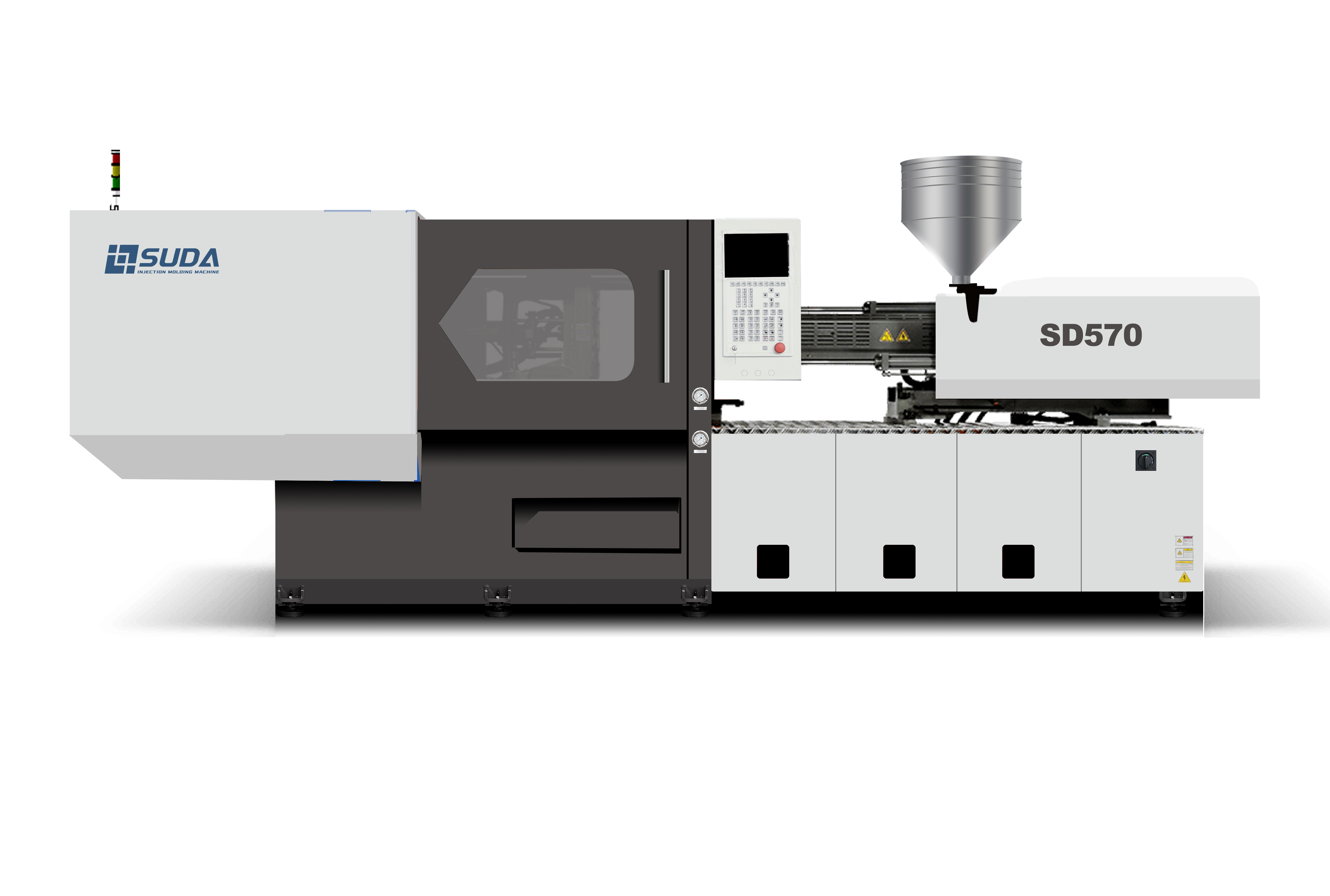
Injection molding process, 13 common product defects and causes