The injection molding machine is mainly composed of four parts: mechanical parts, electronic parts, electrical parts, and hydraulic parts. In addition to most of them, there is an auxiliary part.
1. The mechanical part: mainly consisting of the mold lock part, the glue part and other auxiliary parts.
Model locking section: related to the dribblet cylinder, the dual -song elbow twisting mechanism, the Corinum pillar, the template core.
Plastic parts: arithmetic, tanning cylinder, tube, screw, melting glue motor, fighting, heating element, etc.
Auxiliary parts: racks, safety doors, protective hoods and other related protective devices.
2. Electronic parts: program control electrical appliances, microcomputer control, 2/0 port circuit and drive circuit.
3. Electric section: It is mainly composed of controlling electricity, oil pump motor, electric heating circuit, power circuit, etc.
4. Hydraulic part: It is mainly composed of oil, oil roads, and various oil valves. The oil pressure valve has a proportional pressure valve and proportional flow valve, as well as various electromagnetic control direction valves, overflow valve, etc.
5. Auxiliary parts: mainly consisting of cooling roads, lubricating oil circuits and safety devices.
SUDA introduces the correct operation procedures for the auxiliary machinery and injection molding machine around the injection molding machine:
One, surrounding auxiliary machine
The surrounding auxiliary machine refers to the general term that is directly installed in the injection molding machine or set up in the relevant equipment before and after it, so that the mechanical devices used in the various connected operations of the injection molding machine to automate, save effort and process quality requirements. The peripheral machines that are generally used now can be divided into the following categories according to their functions:
(1) Treatment and supply of molding materials;
(2) The removal and post -treatment of the molding products;
(3) The temperature adjustment of the mold;
Hot Wind dryer dryer
The hot air dryer is the moisture in the raw materials before providing the use of injection molding machines. The working principle of the hot air dryer is to transport the dry hot air through the fan to take away the water in the raw material.
grinder
The crusher crushes the water inlet or bad products appearing during the injection molding process, and it is crushed into a granular material that can be formed again.
Mixer
The mixed color machine adds different raw materials or add various color powder, mother granules and additives to the raw materials for uniform mixing to improve the quality of the product, reduce costs, and reduce manpower.
Automatic filler
The suction machine cooperates with various reserves devices, enter the raw material into the cylinder to ensure the cleaning of the raw materials, reduce manpower, and ensure the safety of materials at high altitudes.
Cold water machine
Cold water machines are used to reduce water temperature, control the mold temperature (3-50 ° C), and ensure the needs of product molding.
Thermostat
The constant thermostat is used to stabilize water temperature or oil temperature, control the temperature of the mold (30-300 ° C), and ensure the need to ensure the molding of the product
Robotic
The robot has taken out the finished products from the mold cavity, saving manpower, improved production efficiency, and improved product molding quality.
conveyor
The conveyor belt is a place where the product is transported to the concentration of the product, saving manpower, thereby improving automated production and improving production efficiency.
Second, the correct operation procedure of the injection molding machine
Preparation before operation
(1) Prepare appropriate tools;
(2) Check the production materials, modify the temperature, pressure and other parameters;
(3) Open the dryer and dry and warm up the plastic.
Check the safety device
(1) Whether the movement of the low -pressure model is normal;
(2) Check whether the safety door protection device is normal;
(3) Check other safety protection devices.
Boot program
(1) Check whether the waterway is completely open;
(2) Check whether each power supply is normal.
(3) Turn on the motor power, turn on the mold, perform clean mold work and mold lubrication.
(4) Check the safety device.
(5) After the temperature reaches the set value, the fight is opened. Remove the overheated plastic in the tube;
(6) Model locking, moving forward, manual, semi -automatic or automatic production.
Shutdown
1. The gates are closed and continued until the product is incomplete, that is, the plastic in the tube is used up.
2. If the work is fully or semi -automatic. Need to switch to manual when the product is incomplete.
3. Clean the mold surface, spray the protective agent, and the mold cannot be high -pressure, and exit the shooting table.
4. Turn off the power supply and total power supply of the machine to clean the fuselage and machine position.
Semi -automatic operation program
Before semi -automatic operation, you can use manual operation several times. When the quality of the product meets the requirements, it can be converted to semi -automatic production.
Full automatic operation program
Before fully automatic production, manual and semi -automatic production must be passed. First of all, check whether the product meets the automatic production conditions. If it meets, it can be used for automatic production after the semi -automatic production is normal.
Model
(1) Power supply, running water, and temperature control power supply;
(2) Select the raw materials and put in the fight;
(3) Check whether the mold can be installed in the injection molding machine;
(4) Check whether the thimble of the mold is consistent with the injection molding stick;
(5) Check whether the tools required for the mold are complete;
(6) The mold is equipped with the width and thickness of the hanging mold to start the motor to adjust the mold;
(7) Measure the width and thickness of the mold, start the motor for adjustment;
(8) Carefully put the mold in the injection molding machine and cancel the high pressure for operation.
(9) Fixed the mold, check the position of the safety rod, and connect the mold to transport water;
(10) Adjust the appropriate locking power;
(11) After the temperature reaches, start manually. After the model is finished.
Correct use of cranes
(1) Pay attention to the maximum weight of the crane and clearly determine the function of each button of the crane before using it.
(2) The crane cannot be affordable for a long time to avoid danger;
(3) When the upper and lower molds, the crane may be suspended, but it is notors to turn off the power to ensure safety.
Adjustment
(1) Select the adjustment mode, cancel the high -voltage position point, straighten the machine hinge, adjust the mold thickness device to the mode of the mold;
(2) Adjust the mold locking itinerary, the position of the thimble, adjust the position of the mechanical protection rod;
(3) Enter the required pressure parameters, adjust the appropriate locking power by adjusting the mold before or after the mold;
(4) Accurately adjust the school care point and mold protective parameters. After the molding is complete.
Undercover program
(1) Disassemble the water transport pipe first, let the water transport, clean the mold cavity, spray the protective agent in the mold, and turn off the mold.
(2) Cut off the motor power, hang the mold with a crane, and remove the code mold.
(3) Open the motor power supply and hang the mold down with slowly.
(4) Cut off the power, carefully hang the mold, and store the mold in an appropriate position.
(5) Turn off the entire power supply of the injection molding machine and clean up the position and the fuselage.
Welcome to Suda Group, ISO9001 Certified
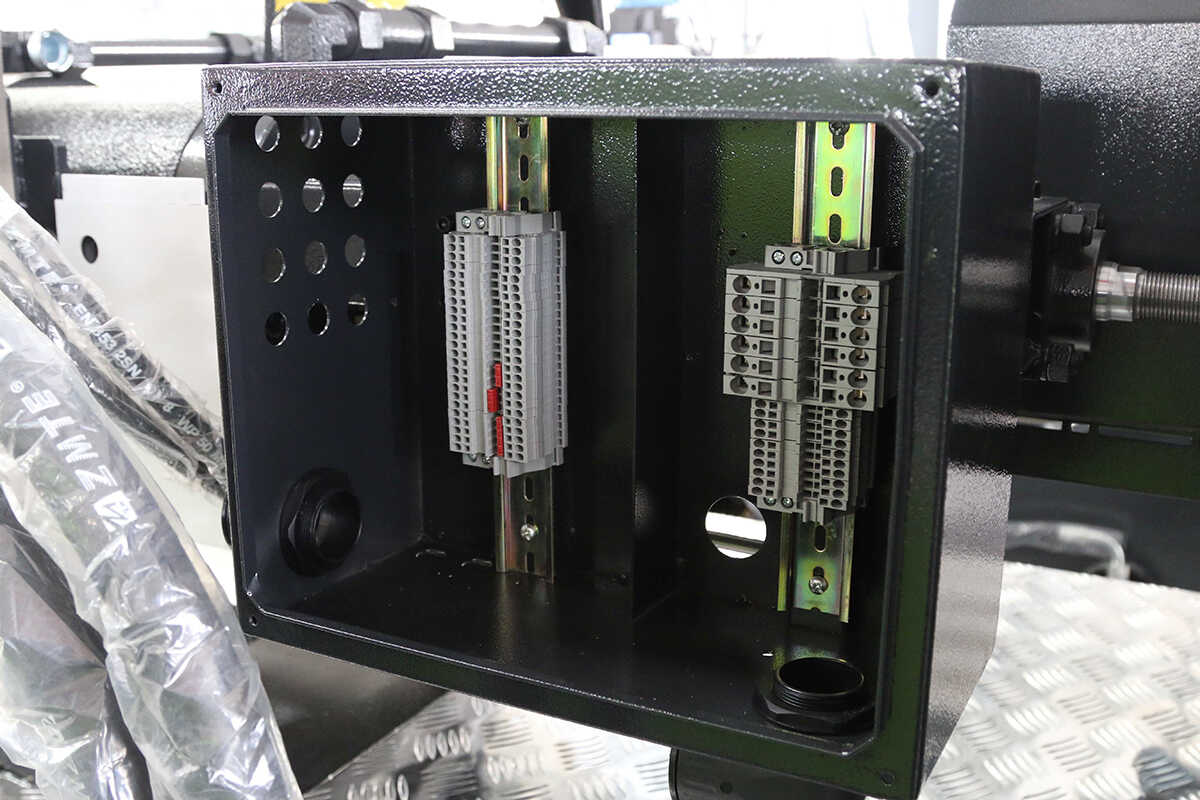
Knowing and operating procedures for injection molding machines