Four common problems of injection molding machines and their solutions
1: Problems and solutions for the failure of the clamping part:
(1): No mode locking:
Approach:
1): Check the travel switch in front of the safety door and repair it.
2): Check the 24V5A power supply in the electrical box, and replace the fuse and power supply box.
3): Check if the valve core is stuck and clean the valve core.
4): Check whether the I/O board has output and whether the solenoid valve is electrified.
5): Check whether the hydraulic safety switch is pressed and whether the mechanical lock lever baffle is opened.
(2): The sound of the mold opening and closing machine:
Approach:
1): Check whether the lubricating oil pipe is disconnected, if so, the oil pipe must be reconnected.
2): If the amount of lubricating oil is small, increase the amount of lubricating oil. It is recommended that 50 molds be oiled once or add enough lubricating oil manually.
3): The clamping force is large, check whether the mold needs a large clamping force, and reduce the clamping force.
4): The current of the amplifier board is chaotic, check whether the current parameters meet the acceptance criteria, and re-adjust the current value.
5): If the parallelism is out of tolerance, use a dial indicator to check whether the parallelism of the first and second plates is greater than the acceptance standard; adjust the parallelism.
(3): Wait a few seconds before opening the mold:
Approach:
1): The starting speed is slow, check whether the screw damping is too large, and adjust the screw damping hole.
2): The middle hole of the damping screw is too large, check whether the damping of the Y hole screw is too large, and replace the damping screw with a thin central hole.
(4): Unlocking the mold and crawling:
Approach:
1): The second plate guide rail and the Colin column are worn out, check the second plate guide rail and Colin column, replace the second plate copper sleeve, Colin column, and add lubricating oil.
2): Improper adjustment of the speed and pressure of mold opening and locking. When the flow rate is set to 20 and the pressure is 99, the second mold clamping plate should not crawl. Adjust the flow proportional valve hole, or the pilot valve hole, and adjust the linear current value of the proportional valve.
3): There is air and exhaust in the pipeline and cylinder.
(5): Open the mold and do not move:
Approach:
1): Increase the speed of mold opening and locking. If the pressure flow is too small, it is not adjusted properly. Check the speed of mold opening and locking and whether the pressure is appropriate. Increase the mold opening and locking pressure and speed.
2): The zero position of the clamping electronic scale is changed, check whether the clamping and straightening machine ends at the zero position after twisting, and re-adjust the zero position of the electronic scale.
3): Check whether the hinge is reversed.
(6): In automatic production, the mold adjustment will become tighter or looser:
Approach:
1): There is leakage in the solenoid valve of mold adjustment, check whether the solenoid valve is "O" type, model 4WE6E or 0810092101, replace the solenoid valve or whether the solenoid valve is powered by 24V when it is not working.
2): Check whether there is a mold adjustment action when manually playing other actions, and see if the valve is stuck.
(7): When other actions are working after clamping the mold, the mold is automatically opened slowly:
Approach:
1): The oil plate is leaking, check or replace the express clamping valve, and replace the oil plate.
2): The mold opening valve leaks, start the oil pump and end the mold clamping, press the injection table or the glue injection action, whether the second plate moves back, and replace the mold opening oil valve. It is normal to open and lock the mold and not move.
(8): When the mold is locked, only the mold opening action is performed:
Approach:
1): connect the wrong wire, check whether there is 24VDC to the valve, check the wire and connect the wire.
2): The valve is stuck or the wrong valve core is installed, check whether the valve core is wrongly installed or blocked, re-install the valve core or clean it. Under normal circumstances, the action of opening and locking the mold is not moving.
(9): Poor mold clamping:
Approach:
1): The A and B holes are not properly adjusted. When the system flow rate is set to 20 and the pressure is 99, observe whether the clamping action is crawling, and readjust or replace the valve.
2): There is air in the oil circuit, listen to the sound of air in the oil circuit, and check whether there are air bubbles in the oil.
exhaust.
3): The ramp-up and ramp-down adjustment of the amplifying board is improper, observe whether the current value of the ammeter is proportional to the rise and fall or whether it is proportional to the rotational speed, and adjust the amplifying board.
(10): Clamping can not afford high pressure, exceeding the stroke:
Approach:
1): The limit switch exceeds the limit, check whether the mold adjustment is appropriate, adjust the appropriate mold thickness; check whether the motor is in normal state.
2): If the hydraulic limit exceeds the stroke, whether the stroke position of the electronic ruler is appropriate, check whether the mold adjustment is appropriate, and properly adjust the mold forward.
2. Problems and solutions for the failure of the mold adjustment part:
(1): Cannot adjust the mold:
Approach:
1): Mechanical level and parallelism are out of tolerance. Check with a spirit level. Adjust parallelism and level. (For large models, small models have little impact)
2): The gap between the pressure plate and the die-adjusting nut is too small. Measure with a feeler gauge. Adjust the gap between the pressure plate and the nut, and the gap between the die adjustment nut and the pressure plate (gap ≤ 0.05mm).
3): Burning the nut: Check whether the nut can be rotated and whether there is iron powder coming out. Replace nuts.
4): Adjust the upper and lower support plates. Remove the bracket lock nut for inspection. Adjust the adjusting nut.
5): The I/O board is broken. Check if there is a signal at the output point on the computer page. Repair electronic boards.
6): The mold adjusting valve core is stuck. Remove valve for inspection. Purge valve.
7): The mold adjusting motor is broken: check the oil motor. Replace or repair oil motor.
Three: Injection part failure problems and solutions:
(1): Can not shoot glue:
Approach:
1): The nozzle is blocked by foreign objects. Check whether the nozzle is blocked. Clean or replace the nozzle.
2): The glue nozzle is broken. Disassemble the flange to check whether the glue nozzle is broken. Replace the glue nozzle.
3): The injection direction valve is stuck. Check whether the directional valve has 24V voltage, and the coil resistance is 15-20 ohms. If it is normal, the valve is blocked. Clean valve or replace directional valve.
4): The injection piston rod is broken. Loosen the rubber injection piston rod tightening nut and check whether the piston rod is broken. Replace piston rod.
5): The barrel temperature is too low. Check that the actual temperature reaches the desired melting point for the material. Reset the barrel temperature.
6): The oil seal of the injection piston is damaged. Check whether the piston oil seal is damaged. Replace oil seal.
(2): The starting sound of plastic injection is loud:
Approach:
1): The injection speed starts too fast. Observe the change of the injection speed at the start. Adjust the injection flow and speed.
2): There is air in the oil circuit. Observe whether there is vibration in each action.
(3): The sound is loud when the glue injection is terminated and the glue is transferred:
Approach:
1): The action transition speed is too fast during injection. Check whether the injection glue has increased the holding pressure. Increase the holding pressure, adjust the injection series, and add the melting delay.
(4): The amount of glue injection is unstable:
Approach:
1): The oil cylinder oil seal is worn. Observe the pressure holding of the pressure gauge. Replace oil seal.
2): The rubber nozzle and the rubber ring are worn. Detected with 2 shots. Replace the three-piece set of dispensing nozzles.
3): The barrel is worn. Detected with 2 nozzles, and simply disassembled to check the wear condition. Replace the melt cartridge.
(5): Semi-automatic without glue injection.
Approach:
1): The advance of the launcher is not terminated. Check whether the travel switch in front of the injection table or mold clamping is normal. Check wiring and travel switch.
2): disconnection. Check wiring. Rewire.
3): Clamping and returning to zero. The position is 0 when the hinge is straightened. Readjust the zero position of the electronic scale.
Four: Hydraulic part failure problems and solutions:
(1): Hydraulic oil pollution:
1): Air is mixed into the oil. Mainly due to poor tightness of pipe joints, hydraulic pumps, and hydraulic cylinders. It is manifested in the presence of air bubbles on the fuel tank.
2): The oil is mixed with water. Will turn the oil into a milky white. The main reason is that the cooler is leaking or the environment is humid.
3): Solid impurities are mixed into the oil. Mainly chips, welding slag, rust flakes and metal powder.
4): A colloidal substance is produced in the oil. The main feast is that the seal is eroded by the oil or the oil is deteriorated, resulting in a jelly-like substance in the oil, which often blocks the small holes.
(2): What effect does temperature have on the viscosity of hydraulic oil:
Effects: 1): When the temperature increases, the viscosity of the oil decreases. Changes in oil viscosity directly affect hydraulic system performance and leakage. (normal temperature is between 30~50℃)
(3): Creeping fault:
Causes: 1): Poor lubrication conditions. A "pause-glide-pause" appears. Increase the amount of lubrication.
2): The hydraulic system is immersed in air. Exhaust is required.
3): Mechanical rigidity reasons. Parts wear and deform, causing changes in friction and crawling. Replacement parts.
(4): After starting production for a period of time, the oil pump beeps.
Treatment method: 1): The quality of the oil suction pipe is not good or the throat code is not tightened. Remove the filter and check for deformation. Whether the oil suction pipe is layered. Replace oil pipe and filter.
2): The filter is not clean. Whether there are too many impurities in the hydraulic oil. Clean the filter.
3): Oil pump wear: Check the oil pump oil distribution plate and rotor end face wear. Replace oil pump.
(5): After the motor starts, the pressure gauge has pressure but no flow.
Treatment method: 1): The DA board is broken, repair the DA board.
2): The overflow valve is stuck. Remove the relief valve for inspection, clean the relief valve or replace the pressure gauge for inspection.
(6): no pressure flow
1): Check whether the rotation direction of the motor oil pump is normal.
2): Check for oil leakage.
3): Check whether there is current in the pressure flow valve.
4): Check whether there is an inner hexagon to withstand the pressure valve core, whether it is pressurized, replaced or cleaned
Welcome to Suda Group, ISO9001 Certified
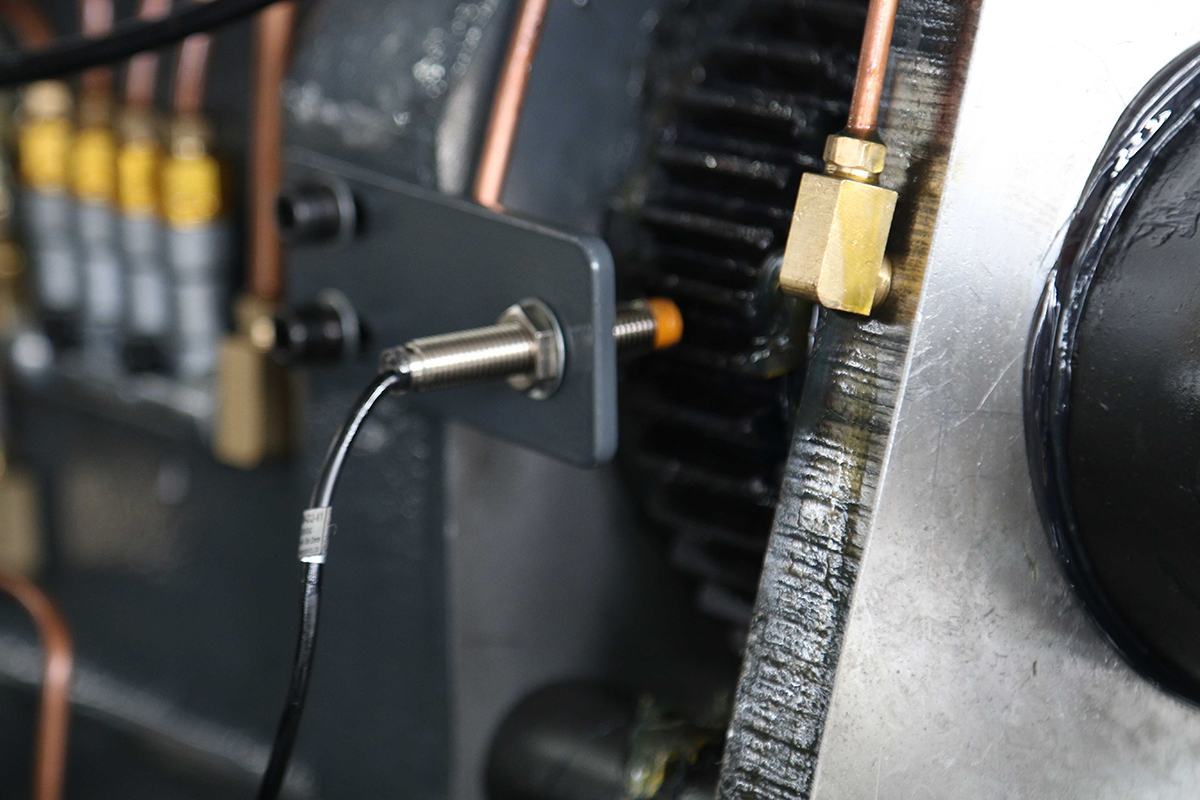
Four common problems of injection molding machines and their solutions