The injection molding process is a complex process that involves many factors such as mold design, mold manufacturing, raw material characteristics and raw material pretreatment methods, molding process, injection molding machine operation, etc., and is closely related to processing environmental conditions, product cooling time, and post-processing technology. process.
Therefore, the quality of the product is not only determined by the injection molding accuracy and measurement accuracy of the injection molding machine, or only by the pros and cons of the mold design and the accuracy level of the mold processing. Usually, it is also affected by the above-mentioned other factors and Constraints.
Under the constraints of so many complex factors, the occurrence of defects in injection molding products is inevitable. Therefore, the internal mechanism of defect generation and the location and type of defects that may occur in products are sought, and used to guide mold design and improvement, and summarize defects. It is particularly important to formulate more reasonable process operating conditions to produce qualified plastic parts. SUDA will introduce the causes of common injection molding defects and how to solve them.
1 Burr (or flash, overflow, overflow)
The occurrence of burrs is caused by the overflow of molten injection molding resin from the parting surface of the mold, and it is a bad state in the molding operation. Especially when the burr firmly adheres to the parting surface of the mold for clamping, it will damage the parting surface of the mold. If the mold is damaged in this way, new burrs will occur in the molded product when reworked. At the same time, it also aggravates the damage of the mold and makes it unusable. So pay special attention.
1.1 Do not use excessive injection pressure
Make the molding machine move at the switching position between injection and pressure holding as soon as possible, reduce the injection volume and reduce the injection pressure. When the injection pressure of the molding machine reaches the set peak value, the resin filling process is completed and the pressure is switched to the holding pressure. When a high injection pressure is applied after the filling process is completed, residual stress is formed inside the molded product and causes burrs to occur.
1.2 Improve clamping force
The clamping pressure can be increased by the clamping pressure regulating valve, or the clamping pressure can be set to 95%. However, an appropriate molding machine should be selected according to the projected area of the molded product and the molding pressure required for the molded product.
1.3 Take good care of the mold
Burrs will definitely occur when the parting surface of the mold is damaged or foreign objects are trapped so that the parting surface cannot be closely fitted. Improper storage of the mold will damage and corrode the movable and fixed mold seat plates of the mold. Therefore, the mold cannot be placed directly on the ground, otherwise burrs will occur when the molded product is formed. It is necessary to develop a good habit of taking good care of the mold. It is also necessary to properly keep the mold mounting surface of the molding machine. Before the mold is loaded into the molding machine, be sure to wipe the mold mounting surface with a rag. In case of rust, knock marks and dents, the solid formwork and lock formwork should be removed, and the milling machine, drilling machine, etc. should be used for processing and repair.
1.4 Adjust the injection volume and reduce the temperature
Burrs can also occur when the shot volume is too large or the temperature of the heating barrel is set too high. The injection volume should be set with gradual increase.
The following methods can also be used to adjust: select high-viscosity grade materials; grind the mold surface where overflow occurs, and use harder mold steel; increase the mold support column to increase rigidity; determine the size of different exhaust grooves according to different materials .
2 Insufficient filling (or insufficient forming)
Insufficient forming is a forming defect caused by cooling and hardening of the molten injection molding resin before it fully fills the cavity. The main reasons are insufficient resin capacity, insufficient pressure in the cavity, insufficient resin fluidity, and poor exhaust effect. When the injection volume of the molding machine is sufficient, and the insufficient molding situation cannot be improved, it should be considered whether the injection pressure is insufficient or the set temperature of the molten resin is low.
In addition, even if the injection pressure is increased and the set temperature of the molten resin is increased when the cavity is not exhausted, insufficient molding will occur. Therefore, attention should be paid to analyzing and judging the situation during molding, and changing the molding conditions such as reducing the injection speed.
When the injection volume of the molding machine is a large value, and the molding temperature and molding pressure are normally set without abnormality, the lack of molding can be solved by selecting a molding machine with an actual injection volume that meets the requirements (or larger).
Check whether the backflow of resin caused by damage and wear of the check ring has occurred, increase the injection amount of molten resin, and when the resin is still terminated at the screw head end, the check ring is damaged.
Due to the occurrence of resin backflow, there are many errors in changing and setting molding conditions. In this case, a resin backflow investigation should be carried out immediately, and the check ring should be replaced. At the same time, the non-return ring should be included in the normal inventory management as a consumable part.
When the temperature of the molten resin is too low, the viscosity of the resin increases, the fluidity deteriorates, and insufficient molding occurs. However, the temperature of the molding resin is still slightly lower than the set temperature required for molding. If the temperature is too high, the shrinkage rate of the molded product will increase, and the forming accuracy cannot be achieved normally. It even causes the resin to decompose and deteriorate until the occurrence of scorch marks and the like.
Insufficient molding caused by the mold, the passing area of the main, runner and gate of the mold is small, the resistance of the resin flow increases, and the complete filling of the resin is also hindered.
In addition, burrs can also occur if the injection speed is too slow. If the forming pressure cannot be increased, insufficient forming may occur.
3 Weld line (or bond line)
Welding marks are thin line-like butt seams formed on the surface of the molded product, which are caused by the cooling of the front end of the molten resin from different directions and the incomplete fusion at the joint. Hard to find if you don't pay attention. Weld lines often occur on the fusion surface of molten resin flowing in the cavity. It mainly affects the appearance and affects the painting and electroplating. In severe cases, it will affect the strength of the product. In order to ensure the quality of the molded product, such defects should be eliminated as much as possible. Adjust molding conditions to improve fluidity.
Such as: increase resin temperature, increase mold temperature, increase injection pressure and speed, etc.
Adding an exhaust groove and setting a push-out rod at the place where the weld line is generated is also conducive to exhausting. Minimize the use of mold release agents. The process flash is set as the place where the weld line is generated, and then it is cut and removed after forming. If only the appearance is affected, the burning position can be changed to change the position of the weld line. Or the part where the weld line is generated is treated as a dark glossy surface, etc., to be modified.
4 depression (or shrinkage pit)
The occurrence of dents is common in surface defects of molded products. It is a defect formed in the wall thickness part due to the volume change caused by the thermal shrinkage of the molded product. Dimples are less severe defects than underforming. It often occurs when the cavity is filled with molten resin, but the holding pressure is insufficient.
The part where the molded product dents occur: when the mold temperature is high, the wall thickness of the molded product; the junction of the molded product wall thickness and the wall thickness (such as the inner side of the reinforcing rib, etc.); when the molded product wall thickness is more than 5mm, the possibility of denting occurs Sex is greatly increased.
When setting molding conditions, in order to prevent the occurrence of dents, it is better to increase the holding pressure. Special care should be taken to prevent the occurrence of resin backflow.
The reason for more dents is that the gate is too small and the mold temperature is too low, so that the resin at the gate is condensed and hardened first. During the pressure holding stage, the shrinking part cannot be supplemented by the molten resin from the gate, which leads to the occurrence of dents. . The solution is to expand the gate, or increase the mold temperature.
5 bubbles
Bubbles are likely to occur in the thicker part of the molded product, and the reason for the formation is exactly the same as the depression of the molded product. What is formed on the surface of the molded product is a depression, and the cavity formed in the middle of the thick wall of the molded product is a bubble. According to the causes of bubbles, the countermeasures are as follows:
When the wall thickness of the product is large, the cooling rate of the outer surface is faster than that of the central part. Therefore, as the cooling progresses, the resin in the central part expands to the surface while shrinking, resulting in insufficient filling of the central part. This condition is called a vacuum bubble.
The main solutions are:
1. According to the wall thickness, determine the reasonable gate and runner size. Generally, the gate height should be 50% to 60% of the wall thickness of the product.
2. Until the gate is sealed, there is a certain amount of supplementary injection material left.
3. The injection time should be slightly longer than the gate sealing time.
4. Reduce the injection speed, increase the injection pressure, and use materials with high melt viscosity.
The main solutions to the bubbles caused by the generation of volatile gases are:
1. Fully pre-drying.
2. Lower the resin temperature to avoid the generation of decomposition gas.
Bubble caused by poor fluidity can be solved by increasing the temperature of the resin and the mold and increasing the injection speed.
6 Warping and deformation
Warpage and deformation of injection molded products are very difficult problems. It should mainly be solved from the aspect of mold design, and the adjustment effect of molding conditions is very limited. When the deformation is caused by the residual stress caused by the molding conditions, the stress can be relieved by reducing the injection pressure, increasing the mold temperature and making the mold temperature uniform, increasing the resin temperature or adopting annealing method.
When the stress deformation is caused by poor demoulding, it can be solved by increasing the number or area of push rods, setting the demoulding slope, etc.
When the cooling method is not suitable, the cooling is uneven or the cooling time is insufficient, the cooling method can be adjusted and the cooling time can be extended. For example, cooling circuits can be placed as close to the deformation as possible.
For deformation caused by molding shrinkage, it is necessary to modify the design of the mold. Among them, it is important to pay attention to make the wall thickness of the product consistent.
Sometimes, as a last resort, it has to be corrected by measuring the deformation of the product and trimming the mold in the opposite direction. Resins with a larger shrinkage rate are generally crystalline resins (such as polyoxymethylene, nylon, polypropylene, polyethylene and PET resins, etc.) than amorphous resins (such as PMMA resin, polyvinyl chloride, polystyrene, ABS resin and AS resin, etc.) deformation is large. In addition, since the glass fiber reinforced resin has fiber orientation, the deformation is also large.
7 silver wire (or silver wire)
The silver-white line marks formed on the surface of the molded product along the resin flow direction are silver wire defects. Mainly due to the hygroscopicity of the material.
When the resin is insufficiently dried, silver wire defects may occur due to evaporation of moisture inside the resin during molding. Therefore, it should generally be dried under the conditions of 10-15C lower than the thermal deformation temperature of the resin. For the PMMA tree wax series with higher requirements, it needs to be dried for 4 to 6 hours.
Especially when using the automatic drying hopper, it is necessary to select a reasonable capacity according to the molding cycle (molding amount) and drying time, and start the drying several hours before the injection starts. Silver wire defects can occur when molten resin is overheated and decomposed. At this time, the set temperature of the heating barrel should be lowered.
If the molten resin stays in the heating barrel for too long, it will decompose, carbonize, and generate corrosive gas. In addition to causing silver wire defects in the molded product, the mold, screw, check ring, etc. will be corroded or even scrapped and must be replaced. New parts are very dangerous.
Inclusion of air can also produce silver wire defects. In order to discharge the gas and air generated during the heating and melting of the resin, it is better to increase the back pressure.
When the injection speed is too fast, silver wire defects will occur. If the gate is too small, the resin passing through the gate will cause the same defect as the nozzle hole diameter is too small due to the effect of high temperature. By reducing the injection speed, the passing resin can be prevented from producing scorch defects.
In addition, the reduction of the occurrence of silver wire defects can be improved by enlarging the gate and nozzle hole diameters. Silver wire defects can also occur when the mold temperature is too low, the gas in the mold cavity is not sufficiently discharged, and there is moisture or dirt attached to the mold cavity.
The use of injection molding processing methods is increasingly widespread, and the quality of products depends on many factors. The appearance of defects in injection molding products is inevitable and there are many kinds. Due to the limited space, only common defects are listed here. The countermeasures still need to be summed up and improved continuously in the future trial mode and production process. In order to reduce the cost of producing qualified products, the application of plastic products can be more extensive.
Welcome to Suda Group, ISO9001 Certified
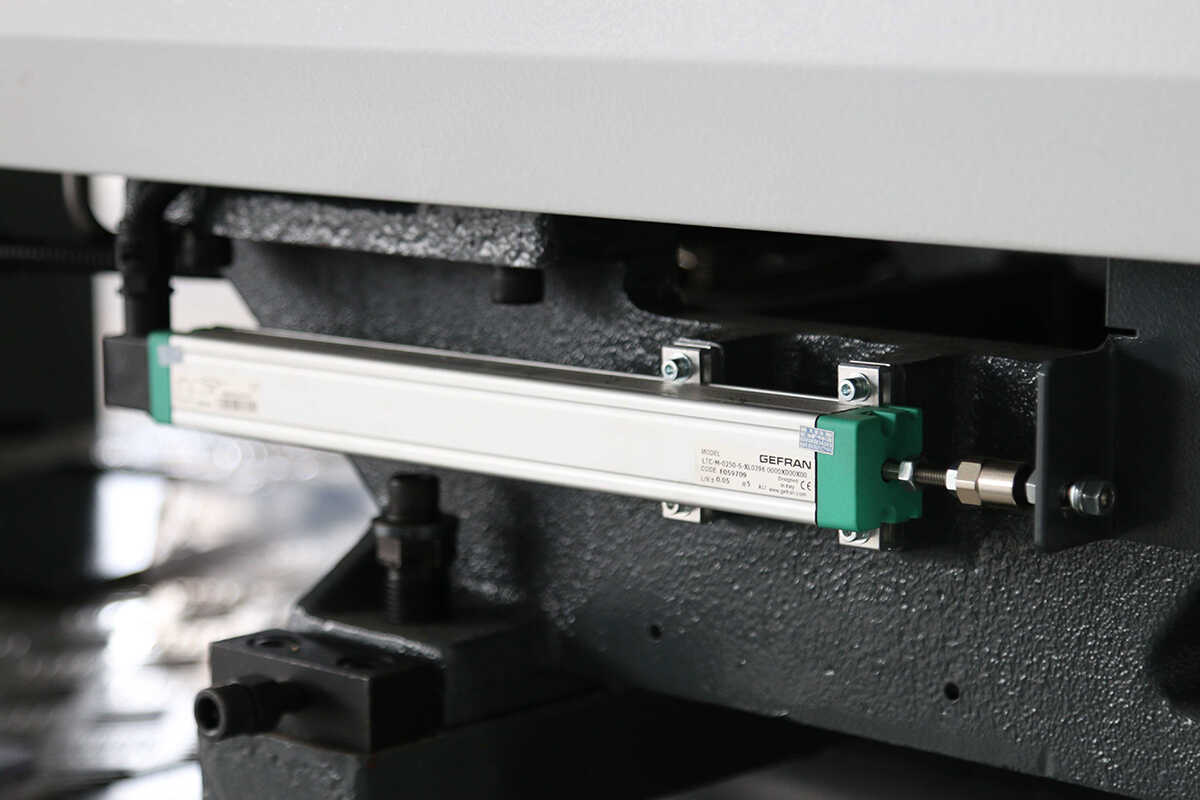
Injection molding problems and solutions